How to Calculate Cost of Goods Manufactured COGM
As we have seen, the total manufacturing cost and cost of goods manufactured are very similar metrics. While accountants can approximate its value at bookkeeping the end of fiscal periods, modern inventory and manufacturing software calculates COGM in real-time, based on actual manufacturing data. Unlike general expenses such as utilities or marketing, COGM sticks strictly to manufacturing costs.
- Unleashed manufacturing inventory software simplifies and accelerates the calculation of COGM by automating data capture, leading to more accurate and timely insights into manufacturing costs.
- It determines the inventory cost at the end of an accounting period and ultimately calculates a company’s gross profit.
- Overstating COGS can underreport taxable income, risking penalties, while understating it could lead to overpaying taxes.
- Without accurate calculation of production costs, a business may end up setting the wrong selling price, which could negatively affect profits.
- Our rigorous editorial process includes editing for accuracy, recency, and clarity.
What type of account is cost of goods sold?
Grouping inventory involves categorizing items by attributes such as product type, size, or batch. This simplifies tracking inventory movements and applying the correct cost to each sale. For instance, a retailer might group clothing by seasonal collections, ensuring items from the same purchase batch are evaluated together for COGS calculations. Simply add your initial inventory, purchases, or manufacturing expenditures, and deduct the finishing inventory.
Cost of Goods Manufactured: Definition and Calculation
These costs can include electricity, water, factory rent, or machine depreciation. Calculating the Coffee Shop Accounting FIFO (First-In, First-Out) cost of goods sold is a key skill for businesses managing inventory. It impacts financial statements and tax calculations by determining which costs are expensed when items are sold. Understanding this method ensures accurate reporting and compliance with accounting standards. You may lower COGS by negotiating better supplier costs, optimizing inventory management, streamlining production, investing in automation, sourcing cheaper materials, and increasing supply chain efficiency. These tactics help to reduce direct costs and increase profitability.
Calculating your Final WIP Inventory
- With a proper monitoring system like the time logs or a system designed to calculate goods completed or a good manufactured, you can know those employees that are slacking and make proper adjustments.
- Understanding the Cost of Goods Manufactured is key for any business looking to improve its bottom line.
- This guide will walk you through the calculation of COGM, its components, and its significance in financial reporting.
- To calculate direct labor, you have to calculate the direct hourly labor rate and the direct labor hours.
- Shopify comes with built-in tools to help manage warehouse and store inventory in one place.
- And with customizable rules, you can categorize transactions your way.
Reducing labor costs is an excellent way to lower the expense of goods manufactured without compromising product quality. Review production processes, reduce waste, cost of goods manufactured negotiate better rates with suppliers, and leverage automation tools like ERP software. This final figure represents the total cost of goods that were completed during the year and ready for sale.
COGM in a manufacturing ERP
Further, this inventory and the COGM value can be used by businesses to determine their cost of goods sold. Like other inventories, the finished goods inventory has a beginning balance for items it didn’t sell before the year’s beginning and an ending balance for items it can’t sell at the end of the fiscal year. How much profit a corporation makes is based on the difference between its costs and revenues. Businesses compute COGM to keep track of their production costs and determine whether they are abnormally high or low in relation to their revenue. In contrast to merchants, manufacturers have special inventory categories including work-in-process (WIP), raw materials, and finished goods.
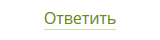